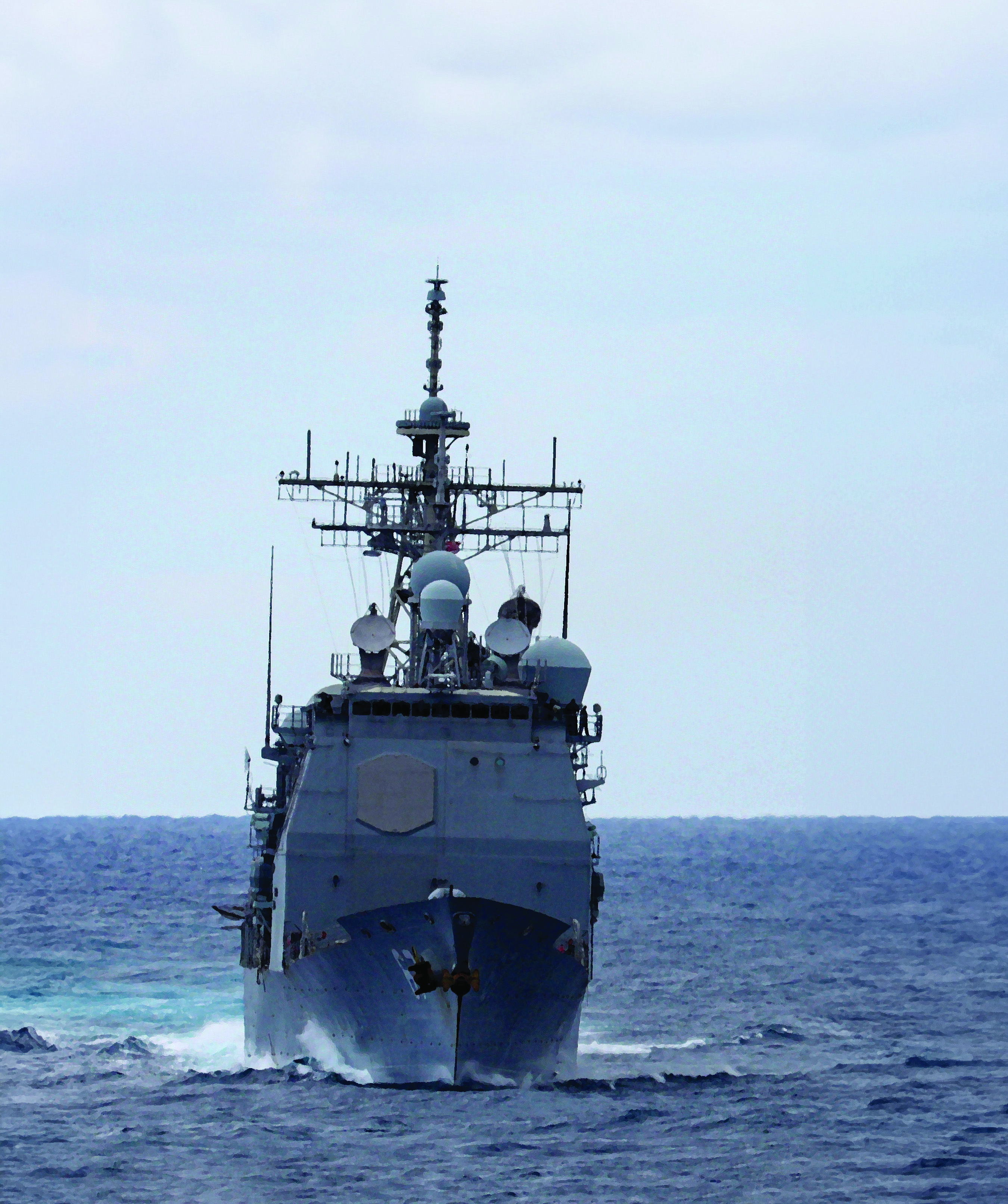
Hutchinson has more than 80 years of experience designing effective solutions to help ensure military technology continues to function properly under stressful and dangerous situations. We know full well how this work can make the difference between a mission’s success or failure, and we take that responsibility to heart.
Challenges in shock protection
When a U.S. Navy contractor needed a shock protection solution for its shipboard identification friend or foe (IFF) device, they reached out to Hutchinson. An IFF is an identification system designed for command and control, using a transponder to identify the broadcaster of an interrogation signal. It enables military interrogation systems to identify aircraft, vessels, vehicles, or forces as either friendly, neutral, or hostile, and to provide their bearing and range from the interrogator. It’s an essential tool for naval operations, and must continue to perform optimally, even in conditions of intense shock and vibration.
The Navy required the system meet Mil-DTL-901E, Grade A requirements, and they were set on using a Cablemount system to provide shock protection for the IFF. The contractor wanted to be sure the system could meet shock-attenuation requirements before moving forward.
Analyzing the Cablemount system
The first step was to set up and run electronic models of the Cablemount solution using BarrySoft Advanced 6 Degrees of Freedom software, providing rigid body shock, vibration, and static force analysis to test a protection/isolation system under different levels of shock. This rigorous modeling method showed the Navy’s recommended Cablemount solution ran far too close to shock limits under testing, with little to no safety factor – leaving no room for possible error.
These results meant the Cablemount system would likely fail in real-life shock testing, risking failure in real-world applications. It was clear ensuring the safety and efficacy of the IFF device in the field meant identifying another option to present as an alternative.
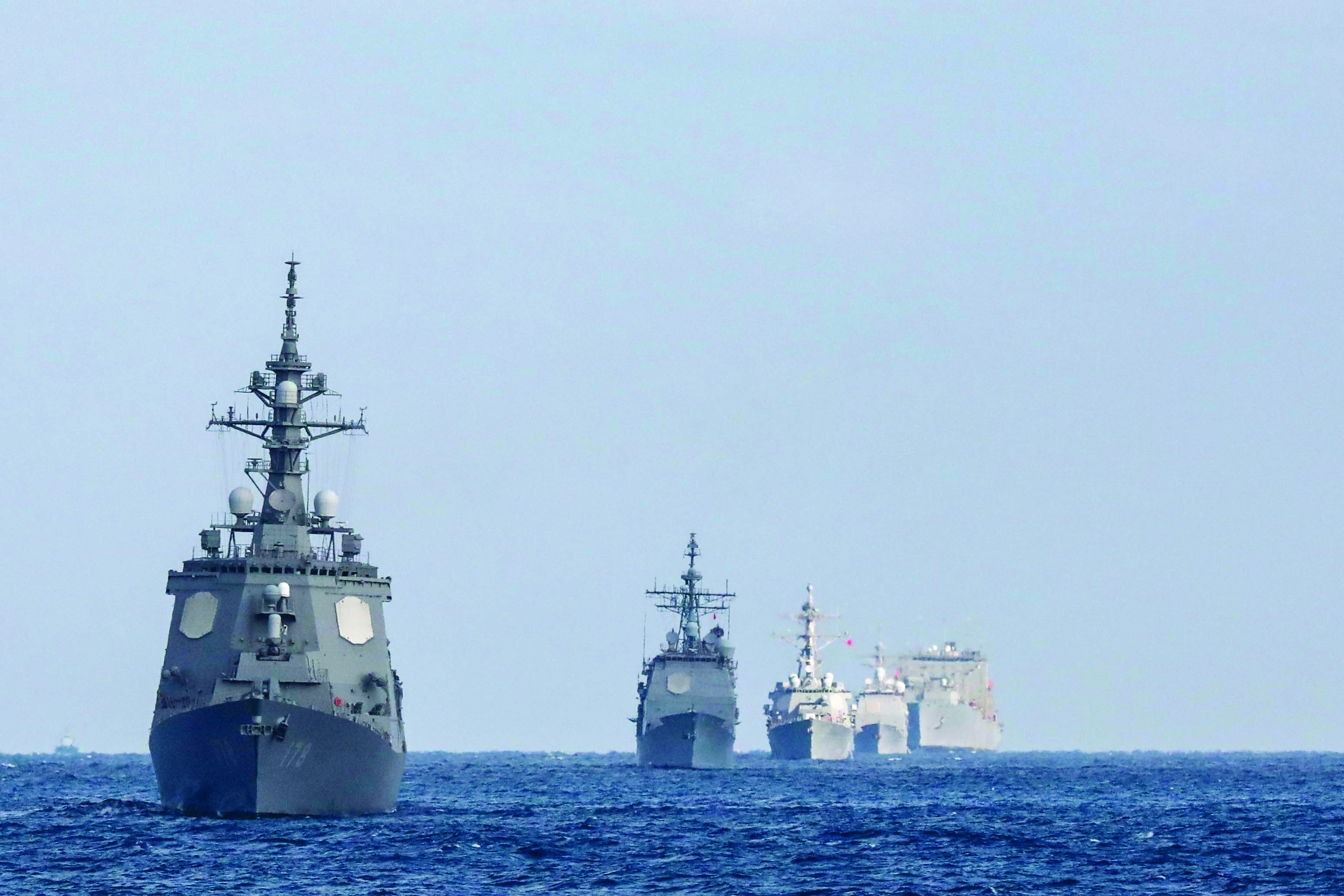
Identifying a superior solution
After continued modeling with BarrySoft Advanced, Hutchinson’s team determined our Very High Capacity (VHC) elastomeric solution was a much more resilient – and safer – solution to provide shock protection for the IFF device. The VHC-Series mounts are special purpose, mid-frequency isolators specifically designed to protect sensitive equipment in situations where high-level shock and vibration inputs are likely. They are used primarily to protect electronic equipment installed in mobile equipment and subjected to off-road environments, such as ground vehicle electronics, shipboard equipment, shipping containers, and equipment installed in transportable shelters.
The VHC elastomeric mount boasts a large deflection capacity to provide superior shock attenuation. It features a buckling design with compression to shear-stiffness ratio of 2:1. It’s made of steel (grounding strap beryllium copper) combined with Barry LT Compound as a resilient element, to operate between -67°F and 180°F (-65°C to 82°C), and remain resistant to fungus and ozone.
Using finite element analysis (FEA) to demonstrate the relative structural integrity of the Cablemount and VHC solutions, Hutchinson presented the results to the customer, explaining how the properties of both solutions contributed directly to the test results.
The DSSM evaluation
Compelled by the data, our customer procured the VHC system to test side-by-side with the Navy’s recommended Cablemount system. The Hutchinson team traveled with the contractor to the National Technical Systems (NTS) in Virginia, where rigorous testing of both solutions was conducted using the Deck Simulating Shock Machine (DSSM).
The DSSM was designed to measure the effects of simulated underwater explosions on electronic equipment, and any new shipboard isolated electrical equipment required to undergo shock testing prior to installation aboard a Navy ship. Naval Sea Systems Command (NAVSEA) engineers use the test results to verify a system’s ability to withstand a shock force from an explosion or blast in accordance with military specifications.

The DSSM for Mil-DTL-901E, Grade A testing confirmed our team’s findings – the Cablemount system quickly broke and failed the shock test. Next up was the VHC elastomeric solution, which made it through DSSM testing successfully with positive results.
Implementation and impact
The customer’s ultimate decision was made for them by the testing and resulting data. The contractor chose Hutchinson’s VHC system to provide the Navy with a solution to reduce shipboard shock levels in its electronics, contributing to long-term safety and efficacy of the ship mounted IFF. Our customer’s custom base system, incorporating our VHC elastomer part, is currently in production.
Because the Hutchinson team identified an existing elastomer product as a viable solution, we saved our customer valuable time and money. Our ability to pull our existing VHC-series mount off the shelf for turnkey use in this application kept the customer’s program on schedule and on budget.
Hutchinson Aerospace and Industry https://hutchinsonai.com
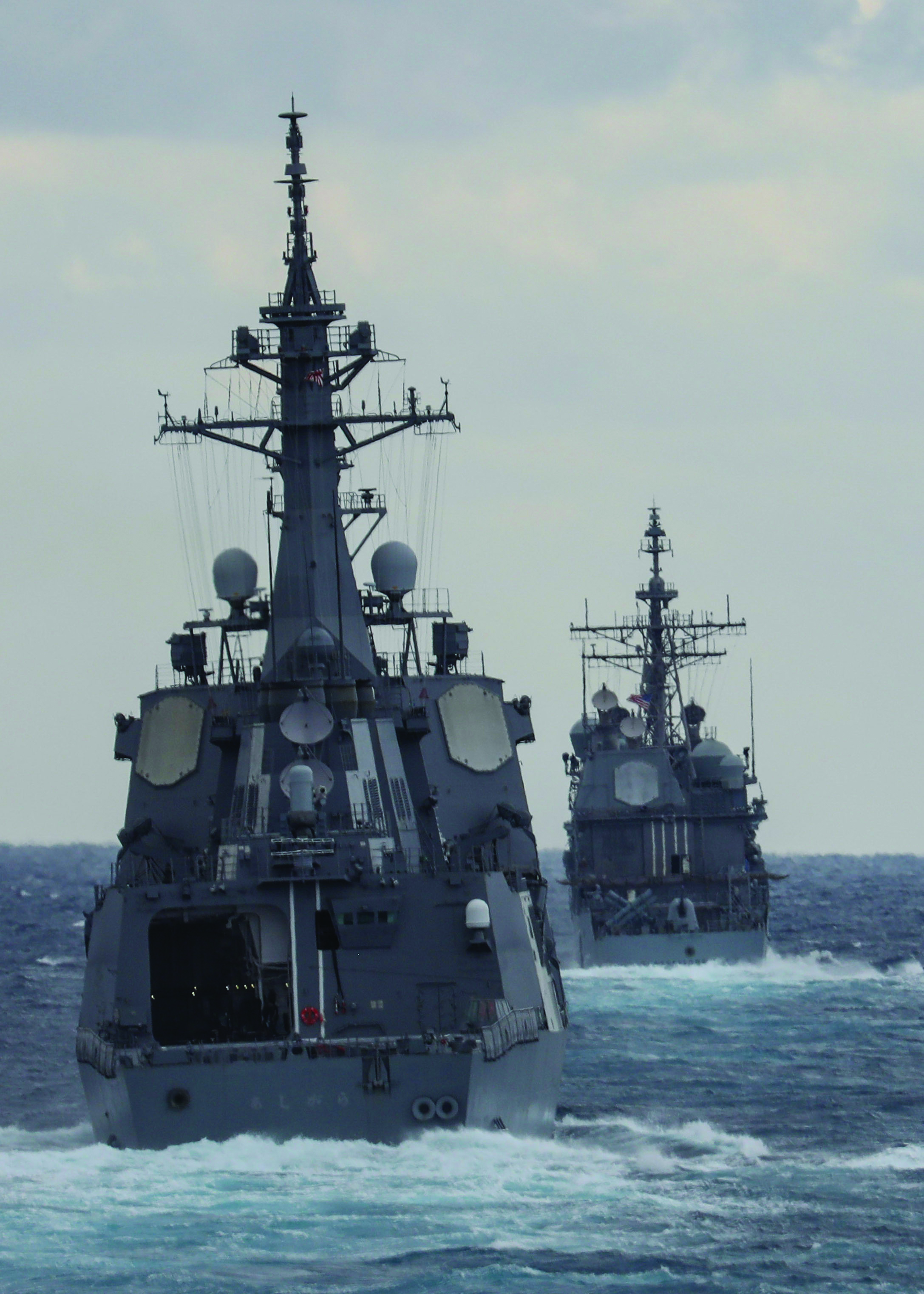

Explore the April/May 2024 Issue
Check out more from this issue and find your next story to read.
Latest from Defense and Munitions
- SWARM Biotactics raised €13M to advance bio-robotics from lab to field
- Teledyne FLIR’s Black Hornet 4 Nano-Drone approved for Defense Innovation Unit’s Blue UAS List
- Hypertherm doubles warranty length for Powermax series
- Tresky's robust DIE bonding and fiber optic technologies
- Signature Engineered Solutions agrees to distribute Unbrako Fasteners across North America
- Down the road: What really is next for electric vehicles?
- Norwegian tech firm Cyvis builds military command center in 24 hours
- Ameresco, U.S. Army’s Detroit Arsenal harness cutting-edge 3D printing to transform building efficiency, sustainability