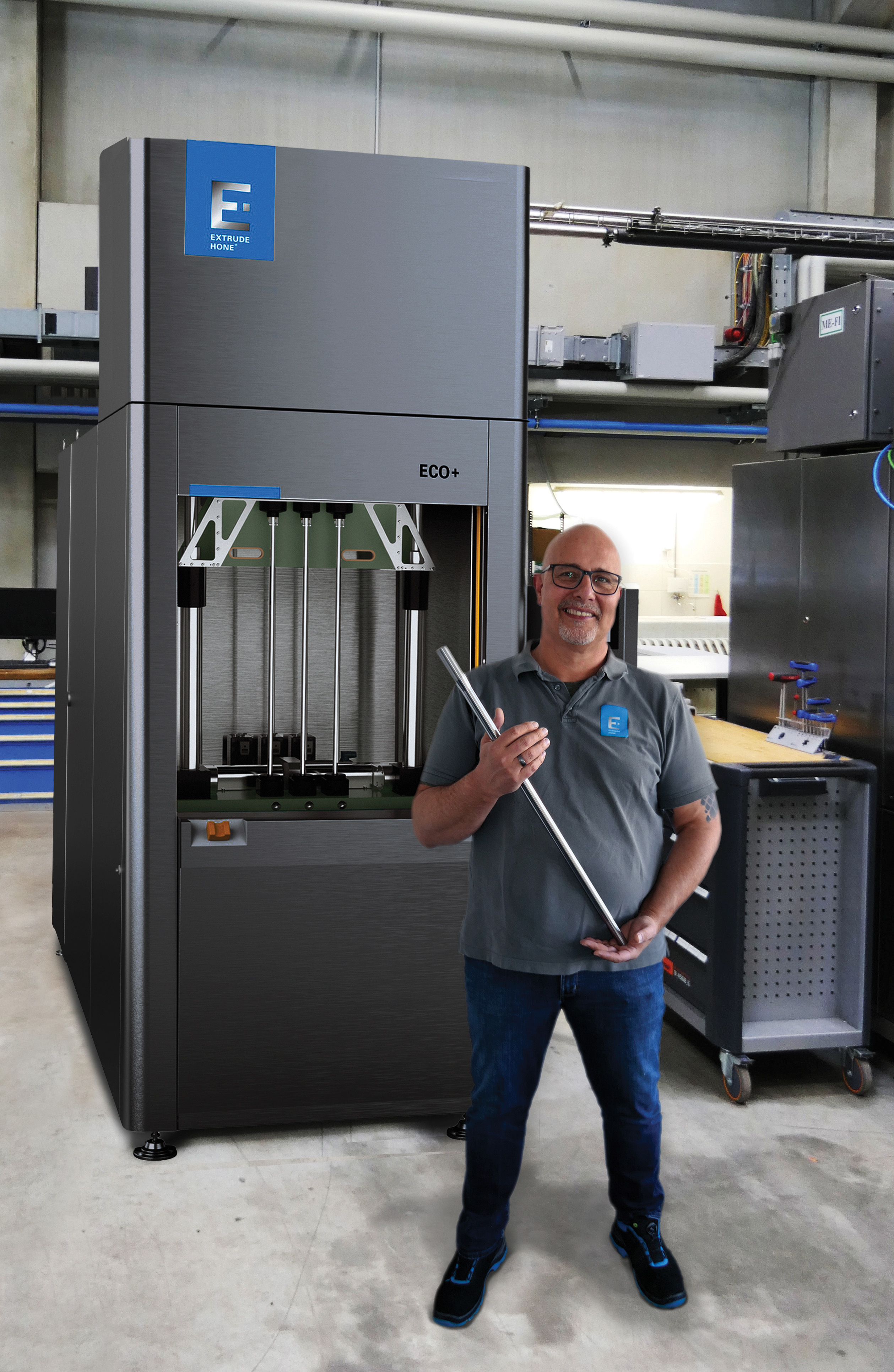
While firearms manufacturers strive for perfection, the devil lurks in the details. Deburring and rifling emerge as critical aspects in this pursuit for the best finish for firearms – particularly crucial when delving into the intricacies of barrel rifling.
Two critical operations – gun barrel polishing and rifling – take center stage in handguns and long barrels.
Rifling is a nuanced process significantly influencing the accuracy and stability of a bullet’s trajectory. The machined spiral grooves within the barrel impart a rotational motion to the bullet upon firing, enhancing its stability and accuracy – factors increasingly critical with greater shooting distances.
A review of the traditional methods of rifling pros and cons offers a better understanding of the benefits of electrochemical (EC) rifling.

Traditional barrel-rifling
Traditional rifling means leverage mechanical rifling, based on cutting or deformation. Some examples include:
Cut rifling, also called hook rifling: A carbide tool generates the groove in several steps, one groove at a time. In comparison to the button rifling cutting, the process creates burrs but less stress. It’s slow and costly because it requires multiple passes to achieve deeper grooves. Cut rifling works well when precision is needed.
Broach rifling: A metal-cutting solution, the broach includes multiple teeth, allowing a single pass instead of multiple ones with the cut-rifling process. It’s an efficient manufacturing process but expensive because of the broaches’ cost.

Button rifling: A cold-forming process pulling the button through the barrel creating lands and grooves. It doesn’t generate burrs but puts stress on the barrel. It’s a prevalent process, especially in manufacturing, by volume, thanks to its short time cycle.
Hammer forging: This pushes a blank on a mandrel and the resulting quality is one asset of this method but it requires high investment.
The science behind EC rifling
EC rifling uses the material’s dissolution and Faraday’s law of electrolysis. The mass of metal dissolving is proportional to the number of electrical charges transferred to the electrode.
Electrolytic machining (ECM) is a subtractive method operating on the principle of anodic metal dissolution via an external DC power source.

One of the critical features of ECM is there’s no contact between the tool (-) and the workpiece (+). The shape of the tool cathode determines the shape of the material removal. ECM is an imaging method. Extrude Hone uses insulating material where no work is needed, leaving the conductive material visible in areas where the material removal process occurs. The groove accuracy depends on the cathode design and the machining precision.
An electrolyte solution (NaCl or NaNO3) handles charge transfer in the working gap to allow the dissolution. The resulting electron current releases metal ions from the workpiece. The removed material comes as hydroxide, is rinsed out of the gap by the electrolyte flow, and must be removed from the electrolyte by an appropriate separating device. Extrude Hone’s process uses a large chamber filter press to ensure a clean electrolyte returns to the machine.
This EC rifling process is a departure from traditional processes as it delivers barrel rifling quality and productivity surpassing conventional capabilities. EC rifling is optimal for superior gun finishing, heightened productivity, and impeccable quality.
Cathodes
The electrochemical process employed by EC rifling ensures creation of precise, polished grooves without any physical contact, applying zero stress to the barrel.
The overall groove geometry is perfectly under control, and the cathode, the tool, isn’t subject to mechanical wear and only some electrical wear. The cathode is consumable.
This approach mitigates concerns associated with traditional barrel rifling methods, where stress and potential deformities may compromise the firearm’s performance over time.
Several cathode designs to produce the grooves are available. Land/groove cathodes and the polygonal design are for static and dynamic EC rifling.

Various barrel configurations
One of the critical advantages of EC rifling lies in its adaptability to various rifling configurations. Whether static or dynamic, Extrude Hone’s EC rifling delivers in conventional rifling with a smooth transition between lands and valleys and polygonal rifling. Polygonal rifling offers benefits such as a better gas seal and reduced stress on the bullet.
Static EC rifling
Static EC rifling is tailored for handguns, providing an ideal solution for shorter barrels. In that configuration, a static cathode seats on the tooling base plate. The principle is to bring the barrel on top of the cathode and immobilize it to ensure good anodic contact. When the barrel is secured, the electrochemical cycle can start. The application’s current requirement, directly related to the surface to be processed, drives the generator capacity. Different generator power sizes allow various current-demanding applications or the possibility of simultaneously processing multiple parts/barrels.
Dynamic EC rifling
Designed to tackle the rifling needs of longer barrels, dynamic EC rifling caters to the diverse requirements of the firearms industry.
In this alternative configuration, the cathode travels down through the barrel at a given feed rate and twists from the top of the machine. When the cathode enters or exits the barrel because of current variation, some potential groove deformation could occur. The tooling includes extra barrel extensions that are continuous with the barrel to absorb the deformation, leaving a perfect barrel. Extrude Hone’s dynamic rifling machine can accommodate three 800mm barrels.
One specific point about dynamic ECM is as the cathode travels back and forth through the barrel, plastic from the cathode glides at the surface of the barrel bore to ensure cathode centering. As a result, the plastic wears out. Using specific materials and cleverly designed removal inserts makes for easy cathode maintenance and reduces the consumable cost per part.
Extrude Hone’s EC rifling offers an efficient and precise rifling process. It takes 70 seconds to do polygonal rifling on an 86mm handgun barrel with consistent, high-quality results.
Benefits of the EC rifling process include:
- No stress is applied to the barrel, eliminating the need for stress relief and manual straightening operation as with the traditional methods.
- The possibility to process different materials (hard or soft) with the same tooling and, in most cases, the same setup.
- Flexibility in a progressive twist, which is impossible with the other methods.
- Productivity, the machine can process three barrels per cycle at a 5" feed rate, almost twice as much as the hammer forge productivity.
Consistent quality for firearms manufacturing
Tailor your machine selection to specific needs. The electrochemical machine should offer versatile configurations for EC rifling, static, or dynamic (up to 800mm barrel length). Regarding large volume production, the machine should be robot loading/unloading ready.
The benefit of an electrochemical machine is the ability to switch from a rifling configuration to a deburring one, depending on the manufacturer.

Imagine you have some gun breech requiring fine selective deburring in specific areas. Extrude Hone systems enable the user to switch from the rifling tooling to the gun breech deburring tooling, select the alternative program from the preset library, and go. From there, users can run different campaigns to maximize assets.
Contract shop opportunity
Contract shop services are available in the U.S. and Europe for those unable to invest. Using our contract capabilities gives customers our experience and support to ensure quick turnaround and uncompromised quality.
At Extrude Hone, our goal is to enhance efficiency and help produce flawless parts.
Extrude Hone https://www.extrudehone.com

Explore the April/May 2024 Issue
Check out more from this issue and find your next story to read.
Latest from Defense and Munitions
- U.S. Army designates type classification milestone for the NGSW Lethality Program
- BAE Systems' facilities are ready to scale to support submarine manufacturing
- Thomson's Movotrak CTU 7th axis cobot extension
- Machining Strategies to Save Time and Improve your Process for MedTech Components with Kennametal Inc.
- IEH Corporation unveils new brand identity
- REPKON USA acquires General Dynamics Ordnance and Tactical Systems Garland Operations
- Lantek and TCI Cutting's automated sheet unloading system
- Lisa Anderson, supply chain & manufacturing expert, introduces services framework