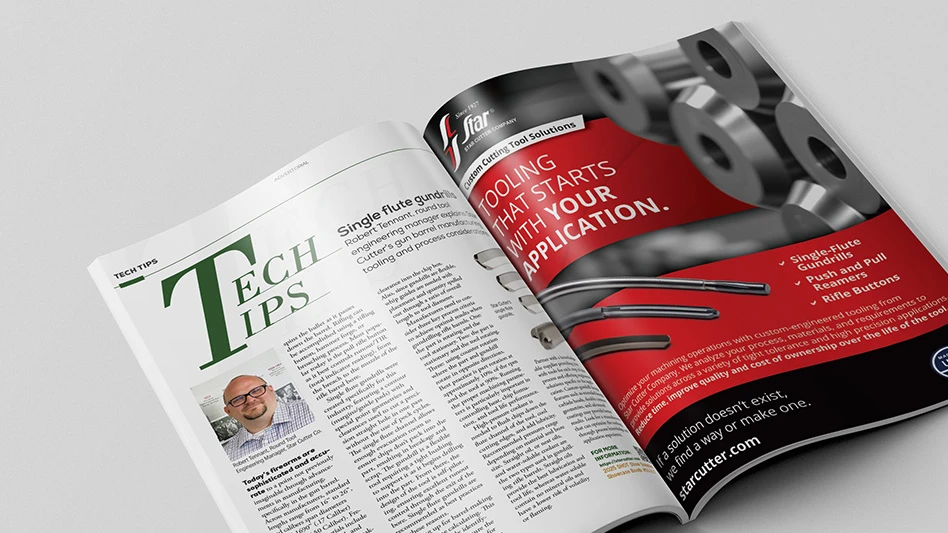
GIE Media

Today’s firearms are sophisticated and accurate to a point not previously imaginable through advancements in manufacturing, specifically in the gun barrel. Across manufacturers, standard lengths range from 16" to 26", and calibers span diameters from 0.1690" (.17 Caliber) to 0.4940" (.50 Caliber). Frequently used materials include 4140 and 4150V steel, and 416R stainless steel. Gunmakers have choices for the best way to produce barrels.
The process for machining the barrel I.D. starts with a gundrill for creating the initial bore, followed by a push or pull reamer to refine the bore hole size further. Last, and key to accuracy, is the rifling, which spins the bullet as it passes down the barrel. Rifling can be accomplished using a rifling button, hammer forge, or broaching process. Most popular today is the pull rifle button as it best controls runout/TIR (total indicator reading), from the breach to the muzzle of the rifle barrel bore.
Single flute gundrills were created specifically for this industry, featuring a contour (margins/guide pads) with special point geometries and clearances used to cut a precision straight hole in one pass without the use of peck cycles. The single flute channel allows enough evacuation room to ensure chips don’t pack into the part, resulting in breakage and scrap. The gundrill is a flexible tool requiring a tight bushing to support it as it begins drilling into the part. From there, the design of the tool is self-piloting, ensuring excellent runout control through the exit of the bore. Single flute gundrills are recommended as best practices for these reasons.
Setting up for barrel-making requires some calculating. This includes properly identifying the length to ensure the gundrill is long enough for the part – as well as for flute clearance into the chip box. Also, since gundrills are flexible, whip guides are needed with placement and quantity spelled out through a ratio of overall length to tool diameter.
Manufacturers need to consider three key process criteria to achieve optimal results when gundrilling rifle barrels. One: the part is rotating and the tool stationary. Two: the part is stationary and the tool rotating. Three: using counter rotation where the part and gundrill rotate in opposite directions. Best practice is part rotation at approximately 10% of the rpm and the tool at 90%. Running the proper machining parameters is particularly important in controlling heat, chip formation, and tool life performance.

High-pressure coolant is needed to flush chips down the flute channel of the tool, cool cutting edges, and add lubricity. Recommended pressures range depending on material and bore size. Straight oil, or neat oils, and water-soluble coolant are the two types used in gundrilling rifle barrels. Straight oils provide the best lubrication and tool life, whereas water-soluble contain no mineral oils and have a lower risk of volatility or flaming.
Partner with a knowledgeable supplier providing you with tools for each step of this process and offering engineered solutions specific to the application. Custom gundrill design features such as extended-length carbide heads, double contour geometries, and advanced coatings may provide better results. Look for a manufacturer that can optimize the tooling through process knowledge and application experience.
FOR MORE INFORMATION:
https://starcutter.com
2025 SHOT Show Supplier Showcase Booth #51317

Get curated news on YOUR industry.
Enter your email to receive our newsletters.
Explore the November/December 2024 Issue
Check out more from this issue and find your next story to read.