
Ajax/CECO/Erie Press (ACE)
For more than 150 years, Ajax/CECO/Erie Press (ACE) has been at the forefront of the forging and forming industry, driven by strategic mergers, technological advancements, and a steadfast commitment to customer success. Through this evolution, ACE has grown into North America’s largest supplier of forging and forming equipment, continually adapting to meet the demands of an ever-changing market.
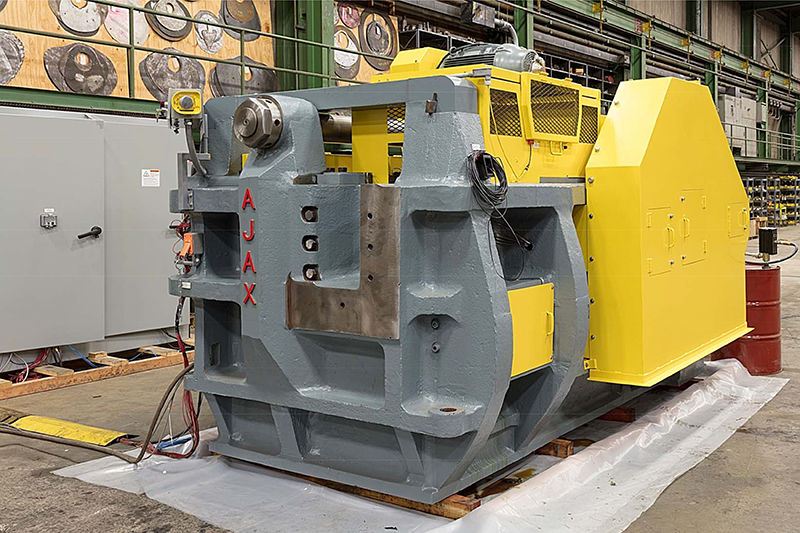
and hydroforming presses, as well as other specialized
equipment.
A major catalyst for this success has been the consolidation of three industry pioneers, bringing together over 400 years of combined expertise. This merger has positioned ACE to offer the most extensive range of forging and metal forming equipment available today. By integrating advanced maintenance and repair programs, state-of-the-art automation and control systems, and comprehensive training initiatives, ACE continues to set new standards for innovation, efficiency, and quality across the industry.
The origins of ACE date back to 1875, when Ajax Manufacturing was established as a pioneering force in the forging industry. Over time, the company built a reputation for producing high-quality forging hammers, presses, and upsetters, paving the way for its future growth.
In 2005, Ajax Manufacturing acquired Chambersburg Engineering Company (CECO), a firm specializing in hydraulic and mechanical forging equipment since its founding in 1897. This acquisition strengthened Ajax Manufacturing’s capabilities in hammer and press technology, broadening its ability to serve a growing customer base with a wider array of forging solutions.
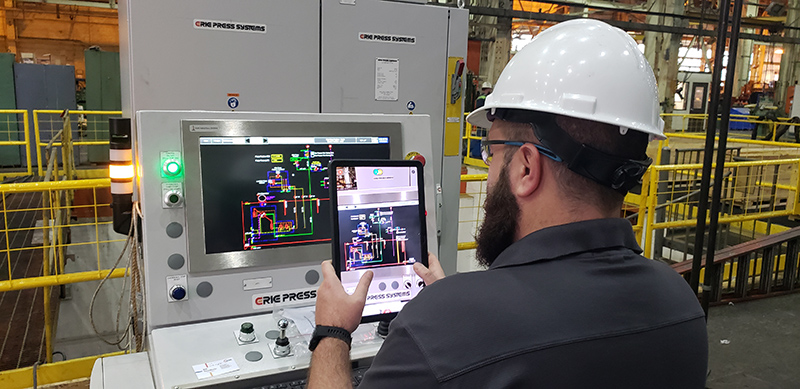
Over the past century and a half, advancements in
equipment, automation and maintenance practices
have enabled manufacturers to improve efficiency,
extend machine lifespan, and enhance workplace safety.
The next significant expansion occurred in 2019 when Erie Press Systems was acquired by Ajax-CECO. Founded in 1895, Erie Press is a recognized industry leader in hydraulic and mechanical press technology, serving critical sectors such as aerospace and automotive manufacturing.
Erie Press specializes in stretch forming, a metal shaping process that involves stretching materials like steel and aluminum beyond their yield point over shaped dies. This technique ensures smooth, precise contours while enhancing strength and minimizing the need for post-processing. Initially developed for aircraft manufacturing, stretch forming has become essential in the automotive, aerospace, and construction industries. It enables the efficient production of complex parts with minimal force, reducing costs and material waste while improving durability and surface finish.
The company is now known as Ajax/CECO/Erie Press (ACE) and continues its leadership in the forging and metal forming equipment industry.
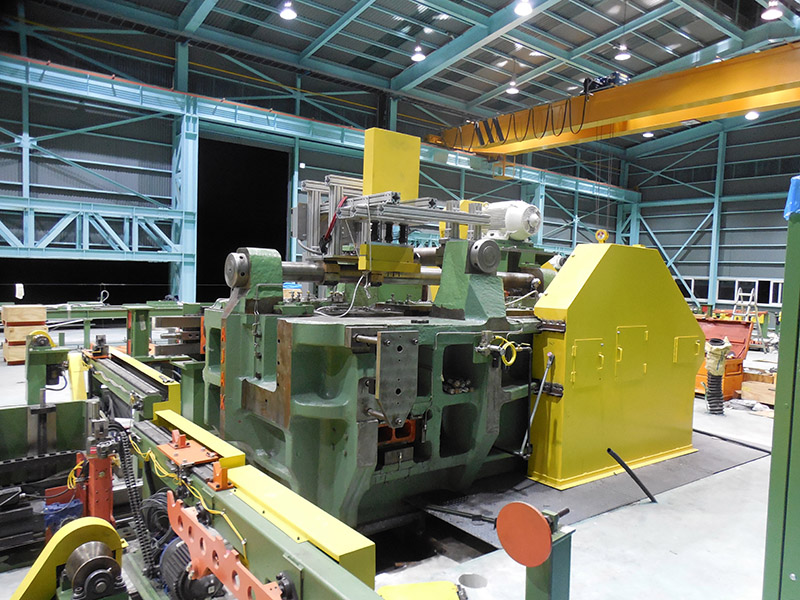
State-of-the-art automation and control systems are utilized
when setting new standards for innovation across the industry.
ACE operates under the umbrella of Park-Ohio Holdings Corp., a diversified industrial holding company headquartered in Cleveland, Ohio. Park-Ohio provides the financial strength and global reach that support ACE’s continuous growth and innovation. Through this partnership, ACE has expanded its engineering capabilities, enhanced its manufacturing operations, and provided customer support across industries worldwide.
As the largest forging and forming equipment supplier in North America, ACE offers a broad spectrum of solutions tailored to meet the needs of modern manufacturing. Its portfolio includes forging hammers, mechanical and hydraulic presses, upsetters, ring rolling mills, and hydroforming presses, as well as other specialized equipment. These machines are integral to industries such as aerospace, automotive, energy, defense, and heavy machinery production.
Although the specific machines may differ, from forging hammers to hydraulic presses, the principles behind their effective operation remain the same. Certain key practices help ensure that equipment performs efficiently, remains operational for longer periods, and meets safety standards. These practices form the foundation of ACE’s approach to equipment support and maintenance, providing manufacturers with structured strategies to reduce downtime and improve productivity.
Across all types of forging and metal forming equipment, ACE emphasizes five core areas: preventive maintenance, repair and spare parts programs, equipment rebuilding and remanufacturing, automation upgrades, and advanced human-machine interfaces (HMIs).
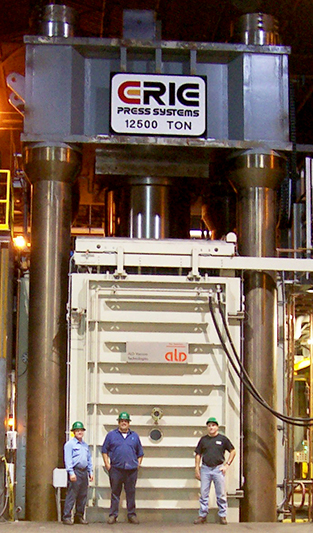
importance of expertise, innovation, and reliability in
the forging and forming industry.
These elements contribute to the longevity and efficiency of industrial machinery by reducing unexpected failures, improving process automation, and enhancing operator control. Additionally, structured training programs help manufacturers address workforce challenges by ensuring that operators and maintenance teams have the necessary knowledge to manage and maintain their equipment effectively.
The 150th anniversary of ACE highlights the enduring importance of expertise, innovation, and reliability in the forging and forming industry.
Over the past century and a half, advancements in equipment design, automation, and maintenance practices have enabled manufacturers to improve efficiency, extend machine lifespan, and enhance workplace safety. As the industry continues to evolve, the value of proven knowledge and well-engineered forging and metal forming solutions remains essential for manufacturers striving to maintain quality and competitiveness.
Latest from Defense and Munitions
- Henry Repeating Arms commits 100% of operations to Wisconsin
- Cortec's corrosion prevention for military readiness
- Pemamak's PEMA Vision 3D software
- Karman Space & Defense acquires Metal Technology Inc. (MTI)
- AV’s one-way attack UAS secures DIU backing under Project Artemis
- Sandvik Coromant's CoroDrill Dura 462
- #56 - Manufacturing Matters - How Robotics and Automation are Transforming Manufacturing
- General Dynamics Electric Boat awarded $1 billion contract for material for Virginia submarines