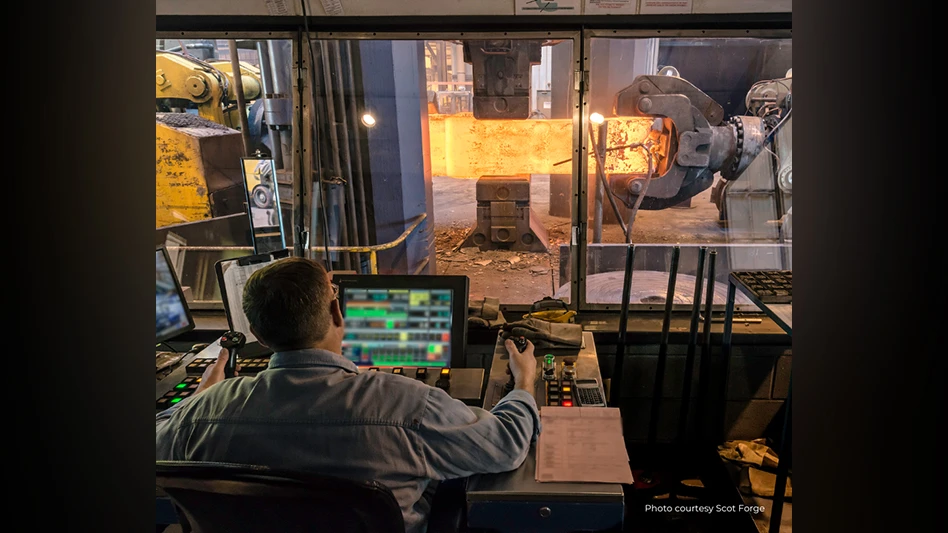
Photo courtesy of Scot Forge
In a significant stride towards addressing the critical workforce shortages in the U.S. casting and forging industry, the Institute for Advanced Composites Manufacturing Innovation (IACMI), in partnership with the Department of Defense’s (DOD) Industrial Base Analysis and Sustainment (IBAS) Program, announced today it has partnered with Pennsylvania State University (PSU), the University of Tennessee, Knoxville (UT), and Jobs for the Future (JFF) to support a groundbreaking national workforce initiative.
With the DOD identifying a pressing need for at least 122,000 additional personnel in vital roles by 2028, the Metallurgical Engineering Trades Apprenticeship and Learning program (METAL) emerges as a strategic countermeasure to fortify national defense through workforce empowerment and technological sovereignty.
METAL is supported by the DOD’s IBAS program, which focuses on strengthening the competitiveness of the U.S. industrial base in response to national security threats and promoting workforce development initiatives. The program seeks to cultivate a resilient domestic workforce capable of sustaining and advancing the nation’s casting and forging capabilities through 2050.
METAL will support a revitalized workforce while addressing vulnerabilities within the U.S. defense supply chain, which can be dependent on foreign sources for cast and forged products critical to warfighting capabilities.
"The shrinking supply chain and shortage of skilled labor demands an immediate response,” says Technical Director of Metallurgy and Manufacturing for the Office of the Assistant Secretary of Defense for Industrial Base Policy Dr. Matthew Draper. “Our partnerships equip us to develop robust training programs that not only meet the immediate needs but also prepare the workforce for future technological advancements. This is something that will provide a cornerstone for the future of the casting and forging sector and provide opportunities for individuals to move into good paying, dynamic, and meaningful careers."
METAL: A Vision for a Strong National Workforce
Rooted in IACMI's proven track record of spearheading successful technical training networks through programs like ACE, this partnership will scale up educational programs focusing on essential base metal processes, including casting, forging, and plate production across the U.S. The goal is to expand the pool of skilled professionals ready to start and sustain a career in the casting and forging industries nationwide. This can be achieved by engaging a diverse audience that includes K-12 students, college and university students, and adults who are either seeking further training or looking for pathways into the industry.
“Fostering development of an industrial base workforce and ensuring the right skill sets are available – from skilled trades on the shop floor through doctorial-level engineering capabilities in a research setting – is vital to national security,” says Joannie Harmon, vice president of workforce development for IACMI. “Our goal for METAL is to ensure the nation’s advanced manufacturing workforce is a source of strategic and competitive advantage for the United States. The foundational building blocks for all manufacturing starts with metal. Supporting the casting and forging sector is a critical role IACMI plays in the creation of a robust talent pipeline with twenty-first century capabilities and skills.”
Pennsylvania, with its strategic position within the base metals manufacturing sector, has been chosen as the site for the METAL testbed. Curriculum will be developed as part of a collaborative effort, and students will participate in a pilot program in casting and forging. Additional training hubs are planned for strategic locations in additional states.
Online and in-person curriculum are being co-developed by PSU and UT for a variety of audiences:
- Outreach events for students as young as elementary age
- 2-3 hour workshops for middle and high school students
- 5-day bootcamps for students age 18 and over
- Metallurgical engineering courses & certificate programs
Additionally, PSU is developing sustainability plans to ensure the continuity and growth of the METAL program beyond the contract period.
For those ready to enter the industry directly, JFF will assist with developing apprenticeship programs and upskilling workers across the country in vital occupational roles. Apprenticeships have proven to help companies recruit, train, and retain a more loyal and productive workforce, which is essential for national security and economic vitality.
Latest from Defense and Munitions
- Overland AI demonstrates soldier-led autonomy across day and night operations
- NOBLE wins Army JPEO CBRND IDIQ contract for CBRN defense
- Kaman Measuring's Precision Measuring Systems for free space optical communication
- Vigilant Aerospace selected for US Air Force contract for uncrewed airspace management
- July is for learning – so drop in for this month’s second Manufacturing Lunch + Learn
- UNITED GRINDING Group and GF MACHINING SOLUTIONS becomes UNITED MACHINING SOLUTIONS
- Teledyne FLIR OEM unveils brand, website to strengthen supply chain, accelerate innovation in infrared imaging
- Essential strategies to protect your data