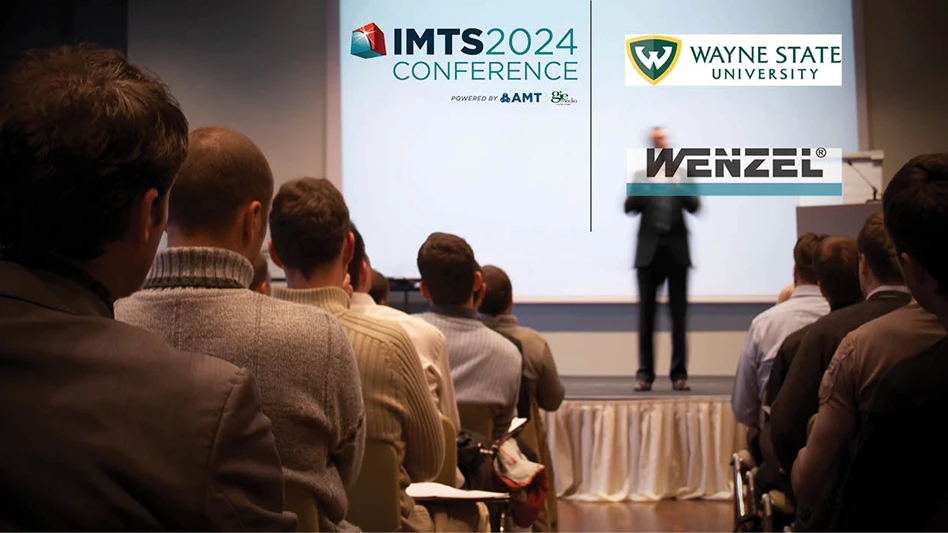
GIE Media's Manufacturing Group
Monday September 9 3:15 PM CST
IMTS13 Room W192-A
About the presentation
Computed Tomography (CT) scanning, as a quality inspection technology, has traditionally been used by manufacturers off-line or in high value/very low volume scenarios due to the considerable time investment needed to gather, process, and analyze data. Increasing the integration of CT scanners in manufacturing environments can provide detailed internal and external digital records of production parts not achievable with current inspection technologies, but this requires the CT scanning process to be less operator-dependent and more traceable. CT scanning pre-scan parameter setting, scanning, and post-scan data processing and analysis can potentially be improved through new computational capabilities, artificial intelligence/machine learning algorithms, and data processing/analysis structures. This paper proposes a machine learning-based recommender system to recommend CT scanning parameters that provide feasible scans, reducing the amount of operator-based scan parameter searching. Since the critical element of this system is a machine learning model that predicts scan feasibility, the developed recommender's performance is evaluated by its ability to predict scan parameters that lead to feasible scans. The accuracy of four machine learning methods on predicting scan feasibility are compared. The multi-layer perceptron approach accurately predicted scan feasibility, with an accuracy range of 0.979 to 0.992, surpassing the other three methods. However, since multi-layer perceptron does not elucidate on the prediction model behavior, a game theoretic approach was utilized to explain the predictions provided by the model. Finally, a two-part experiment to evaluate the performance of the recommender system demonstrated its effectiveness on both familiar and unfamiliar materials.
Meet your presenter
Dr. Jeremy L. Rickli received his B.S. and M.S. Degrees in Mechanical Engineering from Michigan Technological University and received his Ph.D. in Industrial and Systems Engineering from Virginia Tech prior to joining Wayne State in 2013. At Wayne State, he created the Manufacturing and Remanufacturing Systems Laboratory (MaRSLab). MaRSLab targets fundamental and applied research in manufacturing, remanufacturing, and disassembly processes and systems while encouraging considerations for sustainability and life cycle thinking in design, manufacturing, use, and recovery. His research thrusts include: Uncertainty Management in Remanufacturing and Disassembly; Leveraging Data to Innovate Decision Making in the Digital Manufacturing Enterprise; Collaborative Robotic Automation in Advanced Manufacturing and Disassembly Systems. Within these thrusts, he has investigated: disassembly automation for enhanced component and material recovery; integrating disassembly and remanufacturing decisions into product design phases; the interaction between manufacturing operators and collaborative robots; learning programs for the application of collaborative robots in manufacturing; the potential for point cloud measurement data to transform manufacturing quality monitoring and remanufacturing core condition assessment; managing core acquisition in remanufacturing and value recovery considering uncertain core quality, quantity, and timing; and data analytics approaches to innovating Resistance Spot Welding feasibility certification.
Latest from Defense and Munitions
- Air Industries Group secures $11 million US Navy contract for landing gear assemblies
- Booz Allen and Palantir partner to boost U.S. defense
- BAE Systems awarded $2.5 billion in contracts with Denmark and Sweden for new CV90 combat vehicles
- Hive secures DOD contract for deepfake detection
- ModuleWorks' 2024.12 software components
- Sharrow Propeller now available through ADS as an approved supplier for U.S. defense applications
- RTX's Raytheon awarded $590 million production contract for Next Generation Jammer Mid-Band
- Curtiss-Wright’s NXP 16-Core Arm-based VPX single board computer