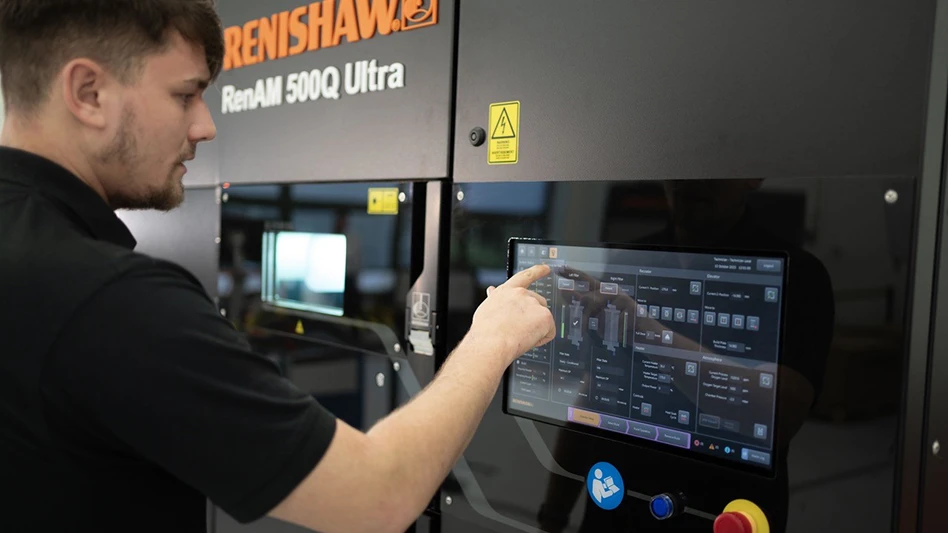
Renishaw
Renishaw features the latest offering in its RenAM 500 series of metal additive manufacturing (AM) systems at SHOT Show 2025, in Las Vegas. With advanced laser technology and intelligent process monitoring capabilities, RenAM 500 series systems deliver unparalleled control throughout the AM process, ensuring consistently high-quality parts. The RenAM 500D is the newest addition to Renishaw’s lineup of laser powder bed fusion (LPBF) systems, and this dual laser option provides exceptional quality and cost-effectiveness at an accessible investment level.
The new RenAM 500 Ultra range of systems, along with the Equator gauging system and the RMP24-micro machine tool probe, are featured in two Renishaw exhibit booths at SHOT (Booth 51610/12 and Booth 55610/12). Visitors to the Renishaw booth will see finished additive parts and learn how the new system delivers significant productivity benefits at a highly competitive price point.
The new RenAM 500D system includes all the existing benefits of the RenAM 500 series, including industry-leading optical, chamber and gas-flow design, and the Ultra model adds new productivity-boosting TEMPUS technology and advanced process monitoring software. TEMPUS technology allows lasers to fire as the recoater moves, removing up to nine seconds of build time per layer. Existing RenAM 500 series customers can upgrade to TEMPUS technology, helping them to make the most of their machine investment.
“Reducing cost per part has always been integral to widening the adoption of AM,” says John Laureto, AMG Americas Business Manager for Renishaw. “Our most recent launches of TEMPUS technology and the RenAM 500D system are focused on productivity, and helping manufacturers reduce build times. As we continue developing systems in the RenAM 500 series, our focus is to lower the entry barrier to metal AM to ensure that manufacturers of any size can find a system that provides value and quality.”
Also on display at SHOT Show 2025 is the Equator gauging system, a proven technology in supporting manufacturers’ drive to develop their own smarter processes and embrace factory automation. Process control is significantly improved with the move from sample inspection to 100% inspection. The Equator system's Process Monitor function displays real-time gauging data bar graphs and charts, allowing for process corrections and scrap prevention. Renishaw’s Intelligent Process Control software (IPC) records actionable data and provides automated real-time solutions, applying offset updates for common causes of instability such as tool wear and thermal drift.
The Equator system, capable of operating at a temperature range of 5 – 50°C and up to 80 percent humidity, is optimized for part loading via a robot or shuttle system. Configured for easy communication between the system and a variety of automated work cell equipment, integration into an automated cell is simplified. The result is significantly reduced cycle times, improved productivity and increased throughput. Introducing flexible gauging close to the point of manufacture also allows the validation of discrete machining operations, which enables automated process control and tool offset management, and increases confidence in final part quality.
Equator gauging systems have been designed to cope with a wide range of parts and design changes, and the system’s automatic stylus changing rack enables inspection of multiple parts in quick succession. It is a proven example of how manufacturers are future-proofing their business activities with an efficient and cost-effective solution to part gauging.
Renishaw will also showcase its latest radio transmission probing system for machine tools at SHOT Show. The RMP24-micro is the smallest wireless machine tool probe on the market, measuring just 24 mm in diameter and 31.4 mm in length. As well as its miniature size, the RMP24-micro also delivers market-leading metrology performance for a wireless probe in this size category. With measurement repeatability of 0.35-micron 2σ and low trigger forces, it is ideally suited to compact machines manufacturing high-value, high-precision components, such as those found in the medical, watchmaking and micro-mechanics industries.
RMP24-micro utilizes Renishaw’s updated radio transmission protocol to communicate with the machine tool controller – via the RMI-QE radio interface. With an operating range of up to 5 meters, it employs a 2.4 GHz frequency hopping spread spectrum (FHSS) protocol, which is industry-proven and compliant with radio regulations worldwide.
Latest from Defense and Munitions
- GE Aerospace receives T700 engine order for Poland's Apache Guardian helicopters
- Raytheon awarded $946 million contract to provide Patriot air defense systems to Romania
- Kays Engineering' gun barrel reaming machine
- Teledyne completes acquisition of Micropac
- Sunnen's HTE-1600W tube hone
- Forge Institute launches Phoenix Xcelerator
- Look into the future of manufacturing in roundtable webinar
- A new chapter for Zagar