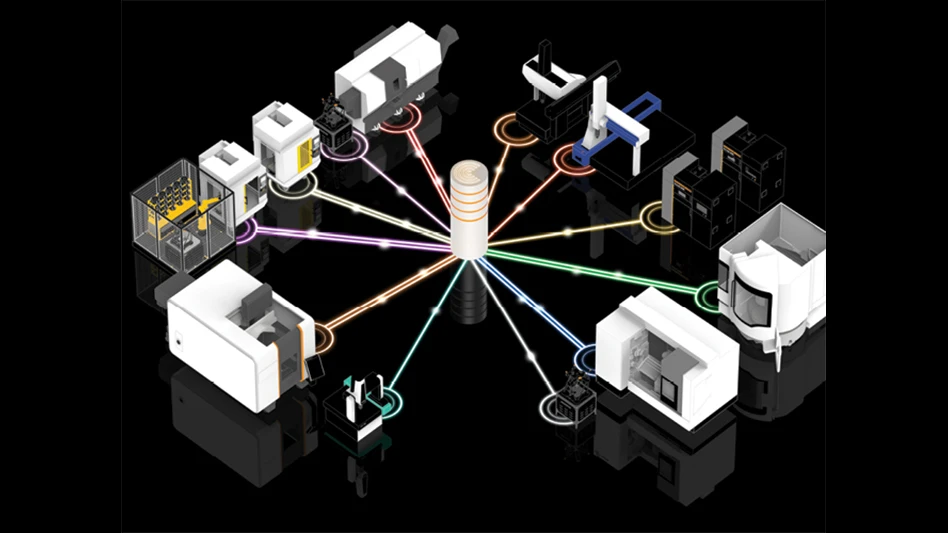
Renishaw

The basic probing system is a machine with a scale system, a workpiece, and a probe connected to a control. The control tells the machine to move the workpiece, table, or spindle, and when the probe comes in contact with the workpiece, the scale system locks in the measurement.

COURTESY OF RENISHAW
This original principle was developed 50 years ago by the founder of Renishaw, Sir David McMurtry, when he was assistant chief of engine design for Rolls-Royce and needed to measure a very thin-walled part when manufacturing the Olympus engines that powered the supersonic Concorde aircraft. At that time, CMMs only had a ball in space which would physically move to capture the measurement – the engineer would touch the part, write down the numbers, and then move to the other side, write down the numbers and do some math to get the diameter or distance between those two measurements. This was problematic for a very thin-walled part because different operators would apply a different amount of force. Over one weekend, McMurtry developed the first touch trigger probe – which produced the same trigger force required for each contact point, locked in that scale reading, and had reliable reproducibility.
Rolls-Royce took out a patent on McMurtry’s original design – filed September 21, 1972 – and McMurtry was acknowledged as the inventor.
McMurtry realized this touch-trigger probe didn’t just solve Rolls-Royce’s inspection issues, it would be able to help precision manufacturers in all markets have an automated CMM. McMurtry, along with John Deer, non-executive deputy chairman at Renishaw, saw this larger opportunity and decided to license the patent from Rolls-Royce for their newly formed company – Renishaw Electrical Ltd.
That was on April 4, 1973. The company’s first order came from LK Metrology and production was moved to Deer’s home garage machine shop. By 1976, Renishaw purchased its first commercial building and grew into the global supplier the company is today.

COURTESY OF RENISHAW

COURTESY OF RENISHAW

COURTESY OF RENISHAW
Beyond the probe
A visit to Renishaw in celebration of their 50th anniversary and for a close look at their manufacturing facilities – plus a preview of their recently released Renishaw Central – was an eye-opening experience.
Renishaw currently has offices in 36 countries, with more than 5,000 employees. Most of the company’s research and development (R&D) and manufacturing is performed in the UK with the company investing roughly 13% of its revenue in engineering which includes R&D. Additionally, as part of the business risk management strategy, the manufacturing sites mirror each other so any catastrophes or natural disasters may disrupt, but won’t halt, production. A range of machine tools support around-the-clock manufacturing operations.
Today, the company’s facilities include:
Miskin, South Wales, UK – 470,000ft2 of space with 620 employees handling machining, electronics, precision and large equipment assembly, 93 CNC machines
New Mills, Gloucestershire, UK – 140,000ft2 of space with 130 employees that houses the head office, R&D, prototyping, new product nursey cells
Woodchester, Gloucestershire, UK – 160,000ft2 of space with 530 employees handling electronics, precision assembly, and distribution
Stonehouse, Gloucestershire, UK – 94,000ft2 of space with 220 employees handling machining, 85 CNC machines
Swords, Dublin, Ireland – 70,000ft2 of space with 140 employees handling precision assembly and distribution
Pune, India – 60,000ft2 of space with 150 employees handling precision assembly

COURTESY OF RENISHAW

COURTESY OF RENISHAW

COURTESY OF RENISHAW
Automating manufacturing
The company’s core machining platform is called RAMTIC, an acronym for Renishaw Automated Milling, Turning and Inspection Centre. RAMTIC, developed in the early 1990s, uses a standard machine tool platform modified for the company’s requirements. The operations include a high degree of automation and closed-loop control supported by Renishaw probing technology for tool setting, in-process monitoring, and component validation.
This vertically integrated manufacturing setup enables the company to provide precision production across periods of unattended operation. RAMTIC is loaded with vertical machining centers configured to accept the company’s custom pallet pools (carousels) which contain the racks for sets of cutting tools and the calibrated artifacts that are used for on-machine verification via probing. The design ensures the carousel’s location aligns with the machine’s transfer position. A trunnion fixture receiver mounted to the table accepts up to 3 standard fixtures at any time. This process enables indexing of parts and fixtures to machine multiple faces in one operation. After the pallet pool is with the machine, no further human intervention is required until part processing is completed.
Because the pallet systems are transportable, kitting – the remote loading of material and tooling – is handled off-line in parallel to machining. This results in quick changeover of products at the machine and minimal spindle downtime. The carousels have 50 spaces and use an indexing chain. Tools are kept on the carousel for off-line tool management. Fixtures are loaded with raw material, billets, strips, or pre-machine parts. Next, the data file is compiled and sent across the network to the machines and then the carousel is moved to the machine using a forklift.
Enabling a wide range of tools to produce different parts, before starting a production run, a rack of tools is transferred into the machine using a pneumatic arm. Tools are then picked from the rack and stored in the standard automatic tool changer (ATC) so the empty rack can be returned to the carousel. Up to 26 tools can be loaded for a carousel run and there are 3 permanent tools in the machine.
Next is the indexer alignment, a critical aspect for part accuracy. A Renishaw probe checks that the indexer axis of rotation point is correct prior to machining and checks that the indexer axis is aligned with the machine axis. This ensures geometric integrity of parts produced along the axis at different angles.
Proper tool setting to ensure accuracy and correct tool placement occurs when the tools are measured for length and diameter offsets. This measurement in the spindle ensures tool or spindle runout is measured at approximately the cutting speed of each tool. Then, actual sizes are compared to reference data. This all happens once at the start of each carousel.
Machining a first-off is done to compensate for any deviation to deliver the highest accuracy machining. Features are produced on one billet and at various index positions. Tools are then checked, and thermal reference points are checked and adjusted before finish machining occurs. Next is part verification, where a probe measures a generic artifact – which is of the same material as the workpiece and with similar geometry and features – calibrated at 20°C with traceability. Parts are measured using gaging points on the machined surface and thermal compensation derived from the artifact is applied to the feature measurement. Subsets of features are also measured for process control.

Renishaw’s Miskin facility.
COURTESY OF RENISHAW

COURTESY OF RENISHAW

Keeping it in-house
The company is committed to manufacturing its own products in-house. At the RAMTIC Miskin facility, beyond machining workers are handling electronic production, precision assembly, as well as assembly of Renishaw’s additive manufacturing machines – the RenAM 500 series. Monthly, the company produces around 1.2 million machined parts, yet they are already outgrowing their current spaces.
So, along with celebrating its 50th anniversary in 2023, the company began expansion plans. Construction is already underway on two halls that will add nearly 550,000ft2 of new manufacturing space to support general capacity increases and large capital goods manufacturing with planned facility occupancy for December of this year. This will nearly double Renishaw’s footprint at its Miskin site.
Additionally, in 2022 Renishaw announced its commitment to achieve a net-zero greenhouse gas emissions target for all its facilities by 2050. By the end of next year, the company plans to have both production halls at Miskin refurbished.
As Renishaw CEO Will Lee explained on the last day of our tour, “The formula that has ensured Renishaw’s success during the past 50 years remains at the heart of our approach to business – investing heavily in R&D to ensure a continuing stream of world-leading products; a commitment to high-quality, in-house manufacturing that ensures we can meet the exacting requirements of our global customers; and a focus on excellent local customer service and support through our wholly owned subsidiary operations.”
Here’s to another 50, Renishaw!
Renishaw
https://www.renishaw.com
Latest from Defense and Munitions
- Is your shopfloor connected? The importance of Industry 4.0 in manufacturing
- BAE Systems selected to enhance ground system for Space Force missile warning satellites
- Gilat receives more than $11 million defense contract from leading UAV company
- Take a lunch break, expand your manufacturing knowledge
- L3Harris marks major milestone for new solid rocket motor ‘Factories of the Future’ in Virginia
- Kopin secures $14 million order for thermal imaging assembly
- ThinKom's ThinAir GT Plus terminal
- Machine Tool Builders Roundtable webinar