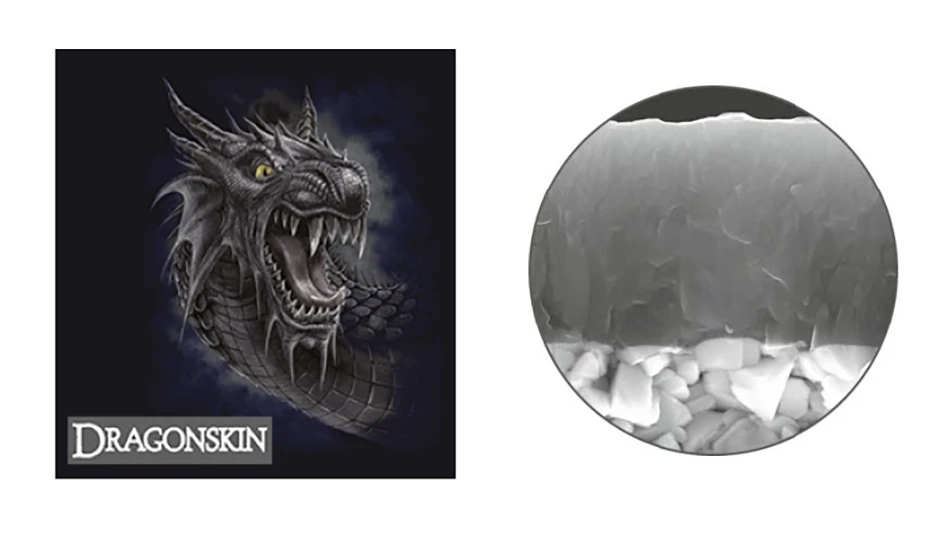
Ceratizit
When it comes to optimum protection against wear, factors such as tool life, temperature resistance and process reliability are paramount. It’s not only the tool geometry that matters, but also the carbide substrate, and the coating and finishing must be perfectly matched to each other. Uncompromisingly designed for optimal protection is the coating technology, Dragonskin, from CERATIZIT.
A multipurpose coating
It’s difficult to find a coating that works for all applications.
"Especially not in such a heterogeneous field as the machining sector," says Dr. Christoph Czettl, R&D manager at CERATIZIT and an expert in coating technology. "Even if wear protection and the associated long tool life are always in the specifications: The choice of material or the machining task in general pose such different challenges to machinists and tools that each individual application has to be considered anew time and again."
CERATIZIT has created a coating family which lives up to the epic name of Dragonskin. As a symbol for the invulnerability of dragon skin, the Dragonskin coating technology offers maximum protection against external influences and effectively reduces premature tool wear.
"Dragonskin is the term we use to describe our entire scientific tool know-how,” says Czettl. “These high-performance coatings are all based on nanolayers, consisting of the appropriate combination of different coating systems and coating technologies."
Layers that count
What is the importance of nanolayers? "They are nanometer-thin layers that are applied alternately. Today, almost all modern coatings are made up of multilayer systems. The advantage of this is that you can combine different properties of different chemical compositions almost freely," explains Czettl.
It’s not just one layer alone that achieves the desired results. Multiple layers each with different properties are needed and combined, they become unbeatable.
“A good example is our CVD cutting material grade CTCM245, which was specially developed for machining high-alloy steels,” says Czettl. “A very tough substrate, an Al2O3 layer, a compound layer and a TiCN layer ensure the best performance.”
Thermal shocks can be effectively avoided and at the same time the CTCM245 is enormously temperature-resistant, which makes higher cutting speeds possible with simultaneously reduced flank and scour wear during the machining of high-alloy steels.
And that’s only one of countless conceivable coating compositions. It all depends on the application and carbide substrate, whether shank tool or indexable insert, either PVD or CVD coating systems and the corresponding coating materials are selected and combined.
"Our basic motivation is to effectively protect tools from wear,” says Czettl. “Some applications may require sharp cutting edges with thin coatings, while others require particularly thick coatings to protect the carbide substrate especially effectively at high temperatures."
Let the chips fall
The best way to protect against heat is to move it away from the tool as quickly as possible. This is why the developers at CERATIZIT have also focused on the after-treatment of Dragonskin.
"With this we achieve extremely smooth surfaces which have a positive effect on the contact friction between chip and rake face - chips are removed more quickly,” says Czettl. “The result is reduced wear with longer tool life and up to 80 percent increased overall performance.”
"Even if many customers don't care what the coating is called or how it’s actually constructed, when they see the Dragonskin logo on our tools, they can be sure that they are relying on the highest performance and the longest staying power,” says Czettl. “Because that's what we research and develop day after day, to make this system that little bit better too."